Wyciskanie części maszyn i wyrobów hutniczych - wszystko co powinieneś wiedzieć.
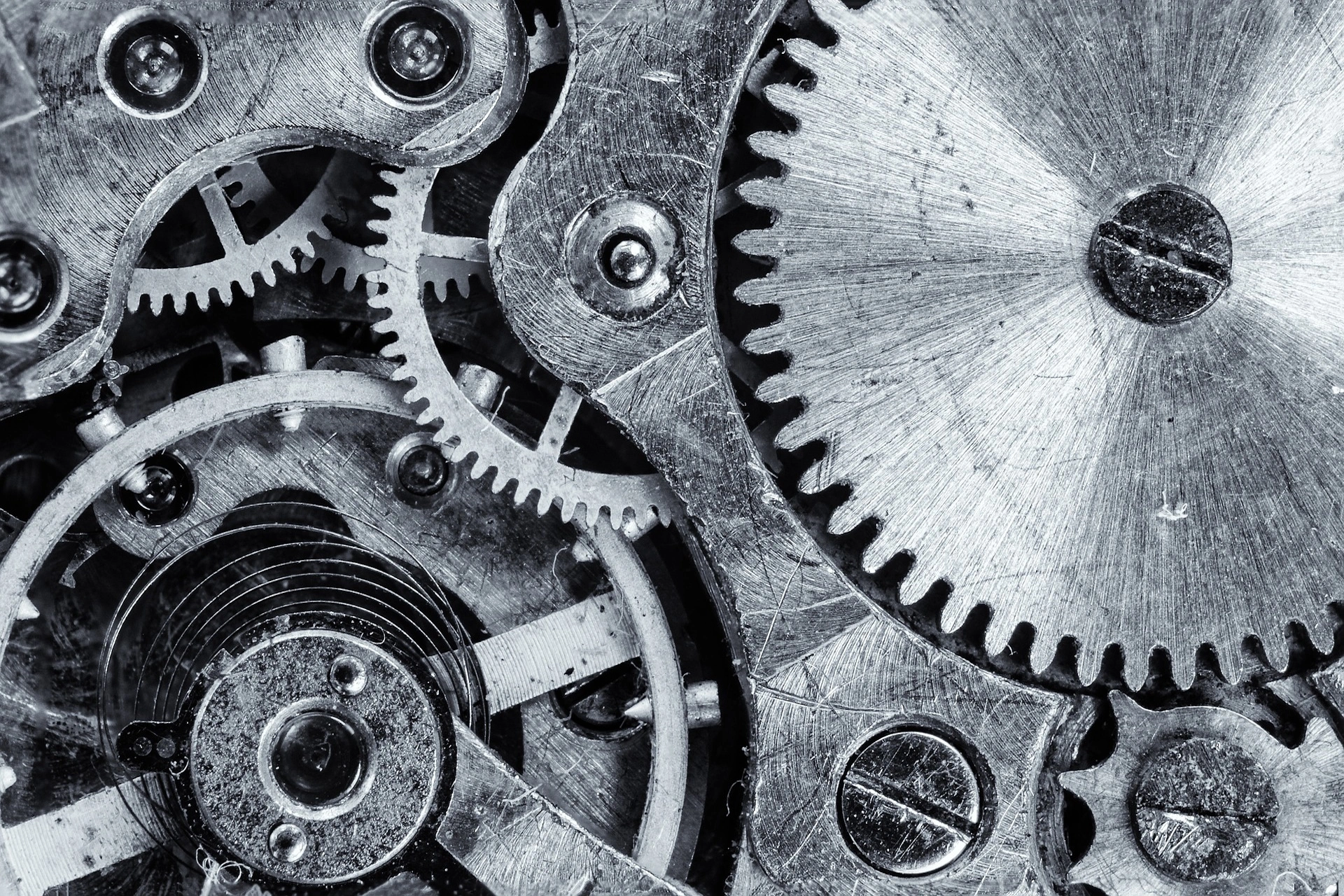
Wyciskanie to jeden z najpopularniejszych i często stosowanych procesów obróbki plastycznej jakiegoś metalu, np. aluminium. W praktyce polega on na wywieraniu przy pomocy specjalnego tłoczyska lub stempla silnego nacisku na materiał umieszczony w matrycy lub pojemniku zwanym recypientem, z których pod wpływem tejże siły „wydostaje” się materiał poddany już obróbce. Początkowo technika ta była stosowana jedynie w przypadku materiałów o stosunkowo niskiej granicy plastyczności, jednak wraz z jej rozwojem, a także w wyniku ulepszenia wykorzystywanych narzędzi – stało się możliwe poddawanie takiej obróbce również stali i innych twardych metali.
Gdzie sprawdza się technika wyciskania?
Wyciskanie to metoda, którą wykorzystuje się przede wszystkim podczas produkcji prętów, rur i części maszyn wykonanych m.in. ze stali. Jednak technikę tę stosuje się także w przypadku materiałów o niskiej plastyczności, których nie można odkształcać, jak również podczas produkcji wyrobów o złożonych kształtach, kilku warstwach różnej grubości oraz tych, w których przypadku inna obróbka byłaby po prostu nieopłacalna ze względów ekonomicznych. Wyroby wykonane techniką wyciskania cechuje nie tylko gładka powierzchnia, ale również precyzyjna dokładność wymiarów oraz dobre własności mechaniczne.
Zalety wyciskania wyrobów hutniczych
Jak się okazuje, technika wyciskania jest wyjątkowo opłacalna zarówno jeśli chodzi o zużycie materiałów, jak i wykorzystanie energii potrzebnej do wykonania obróbki. Daje bowiem szansę maksymalnego wykorzystania powierzchni obrabianego materiału przy stosunkowo niskim zużyciu energii. Co więcej, technikę tę można stosować zarówno na ciepło (przy wykorzystaniu wysokich temperatur), jak i na zimno (bez poddawania materiału obróbce termicznej), a jej dokładność jest porównywalna z precyzją szlifowania i skrawania.
Rodzaje wyciskania ze względu na temperaturę
Główny podział dotyczący tej techniki obróbki dotyczy temperatury wykorzystywanej podczas pracy. Wyciskanie na zimno, a więc takie, podczas którego materiał nie jest poddawany obróbce termicznej, jest stosowane przede wszystkim w przypadku części maszyn oraz takich wyrobów, przy których wymagane są m.in. precyzyjny kształt, gładka powierzchnia i wysoka jakość. Wyciskanie na ciepło przy wykorzystaniu umiarkowanej temperatury stosuje się natomiast w przypadku wyrobów, które podczas wyciskania muszą być poddane znacznie silniejszemu odkształceniu. Wyciskanie na gorąco wiąże się z użyciem bardzo wysokiej temperatury i stosuje się je w przypadku wyrobów, które następnie poddawane są kolejnej obróbce. Te jednak charakteryzują zwykle mniejsze własności mechaniczne, gorsza jakość oraz liczne wady.
Rodzaje wyciskania ze względu na ruch stempla oraz kształt otrzymywanych wyrobów
Innym podziałem związanym z techniką wyciskania jest podział ze względu na kierunek ruchu stempla i wypływania materiału. Biorąc pod uwagę obydwa kierunki możemy wyróżnić trzy sposoby wyciskania – współbieżne, gdy stempel i materiał poruszają się w tym samym kierunku, przeciwbieżne, gdy materiał płynie w kierunku przeciwnym do ruchu tłoczyska oraz boczne, gdy materiał płynie poprzecznie w stosunku do stempla. Wyróżnia się również wyciskanie złożone, gdy materiał poddawany obróbce płynie zarówno w kierunku zgodnym, jak i przeciwnym do ruchu tłoczyska. W przypadku podziału ze względu na kształt otrzymanego wyrobu wyróżnia się pręty, rury oraz naczynia.
Specjalne metody wyciskania
Technologia wykorzystywana w procesie wyciskania jest coraz bardziej zaawansowana i dla zwiększenia efektywności całego procesu stosuje się dodatkowe narzędzia oraz materiały. Do specjalnych metod wyciskania można zaliczyć m.in. metody hydrostatyczne, Conform, KOBO oraz odlewanie ciągłe, podczas których wykorzystuje się koło cierne, kilka zestawów tworzących pojemnik i tłoczysko o bardzo zaawansowanej konstrukcji czy choćby odpowiednią ciecz, która naciska na materiał, dzięki czemu istnieje możliwość zmniejszenia siły nacisku stempla.